Deformations in 3D modeling refer to the process of manipulating the shape or structure of a three-dimensional object. In Blender, deformations play a crucial role in achieving realistic and dynamic models. There are various techniques and tools within Blender that allow artists to deform objects in a controlled and artistic manner.
- Basic Transformations:
- Translation: Moving an object along one or more axes.
- Rotation: Rotating an object around its center or a specific pivot point.
- Scaling: Changing the size of an object along one or more axes.
- Mesh Deformations:
- Vertex Editing: Blender allows users to directly manipulate individual vertices, edges, and faces of a mesh. This provides fine-grained control over the shape of an object.
- Proportional Editing: This feature allows users to influence nearby vertices when editing one, creating smooth and natural deformations.
- Modifiers:
- Subdivision Surface: Smoothens surfaces by subdividing the mesh, resulting in a more detailed and refined appearance.
- Armature (Skeleton): Using an armature (a skeleton of bones) to deform a mesh. This is particularly useful for character animation.
- Lattice: A lattice is a three-dimensional grid that can be used to deform a portion or the entirety of a mesh, providing a non-destructive way to shape objects.
- Soft Body and Cloth Simulation:
- Soft Body: Simulates the elasticity and softness of objects, allowing them to deform realistically in response to forces.
- Cloth Simulation: Mimics the behavior of fabrics, accounting for factors like gravity and wind. This results in natural-looking deformations in cloth-like materials.
- Shape Keys:
- Basis Shape: The original shape of the object.
- Shape Keys: Different deformations or shapes that can be stored and blended with the basis shape. This is useful for creating facial expressions or morphing between different forms.
- Weight Painting:
- Vertex Groups: Assigning specific vertices to groups and controlling the influence of deformations through weight painting. This is commonly used with armatures for character rigging.
- Sculpt Mode:
- Blender includes a Sculpt Mode where users can use brushes to push, pull, and smooth the surface of a 3D model, allowing for organic and artistic deformations.
- Constraints:
- Limit Distance: Restricts the distance between two objects or parts of an object.
- Transformation Constraints: Limits the range of motion for an object.
Understanding and mastering these deformation techniques in Blender allows 3D artists to create realistic and expressive models, whether it be characters, environments, or objects. The combination of these tools and methods provides a versatile and powerful set of features for achieving a wide range of visual effects in 3D modeling and animation.
Mesh Deformation Techniques
Mesh deformation techniques are essential in 3D modeling to manipulate the shape and structure of a mesh, enabling the creation of dynamic and realistic objects. These techniques are particularly valuable in character animation, simulations, and other scenarios where objects need to change form or respond to external forces. Here are some common mesh deformation techniques:
- Vertex Editing:
- Description: Directly manipulating individual vertices of a mesh.
- Application: Artists can use vertex editing to finely control the shape of a model. This technique is particularly useful for detailed adjustments and refining the overall structure of a mesh.
- Proportional Editing:
- Description: Influencing nearby vertices when editing one vertex.
- Application: Proportional editing is beneficial for creating smooth and natural deformations. It allows artists to affect a broader area of the mesh while focusing on a specific point, making it easier to achieve organic shapes.
- Edge and Face Extrusion:
- Description: Extending edges or faces of a mesh.
- Application: Extrusion is commonly used to add detail and complexity to a model. It is effective in creating protrusions, such as limbs or branches, and building intricate geometrical structures.
- Sculpting:
- Description: Using sculpting tools to mold the surface of a mesh.
- Application: Sculpting is an artistic and intuitive way to deform meshes, especially for organic shapes. Artists can use brushes to push, pull, smooth, and add details to a model, making it a powerful technique for character modeling and environmental design.
- Lattice Deformation:
- Description: Using a lattice, which is a 3D grid, to deform a portion or the entirety of a mesh.
- Application: Lattice deformation provides a non-destructive way to modify the shape of a mesh. Artists can manipulate the lattice, and the enclosed mesh deforms accordingly, making it useful for both organic and hard surface modeling.
- Armature Deformation (Rigging):
- Description: Using an armature, or a skeleton of bones, to deform a mesh.
- Application: Rigging is fundamental in character animation. Artists define how the mesh should deform by assigning vertices to bones. The movement of the bones then influences the shape of the mesh, allowing for realistic character animation.
- Shape Keys:
- Description: Storing and blending different deformations with a basis shape.
- Application: Shape keys are beneficial for creating facial expressions, morphing between forms, or animating gradual changes in a mesh’s shape. They provide a way to store and interpolate between different configurations.
- Weight Painting:
- Description: Assigning weights to vertices to control their influence during deformation.
- Application: In rigging, weight painting is crucial for defining how much each bone affects specific parts of a mesh. It allows for precise control over the deformation of complex shapes, such as characters with intricate facial expressions.
Mastering these mesh deformation techniques in 3D modeling software like Blender empowers artists to bring their creative visions to life by sculpting, animating, and simulating objects with a high degree of realism and expressiveness.
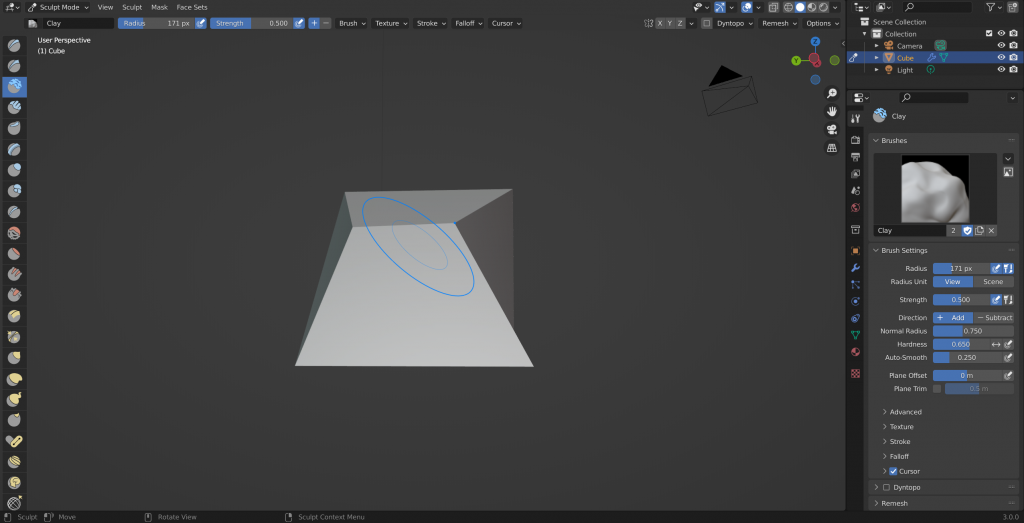
Other Application Of Deformations
Deformations find wide applications across various fields, enhancing the realism and versatility of 3D models. These applications range from entertainment and gaming to scientific simulations and industrial design. Here’s an overview of how deformations are applied in different domains:
- Entertainment and Animation:
- Character Animation: Deformations, especially through rigging and skeletal animation, are crucial for bringing characters to life in movies, TV shows, and video games. Artists use techniques like blend shapes and bone deformations to create lifelike movements and expressions.
- Special Effects: Deformations are employed in simulations for effects like cloth, fluid dynamics, and soft body physics to achieve realistic visual elements in scenes.
- Gaming:
- Character Rigging: In the gaming industry, deformations play a vital role in character rigging for both player characters and non-player characters (NPCs). Rigging allows characters to move dynamically in response to player actions.
- Environment Animation: Deformations are applied to create dynamic and interactive environments, such as swaying trees, flowing water, or deformable terrain.
- Virtual Reality (VR) and Augmented Reality (AR):
- Real-Time Deformations: In VR and AR applications, real-time deformations are used to enhance user immersion. Dynamic interactions, deformable objects, and realistic animations contribute to a more convincing virtual experience.
- Product Design and Industrial Simulations:
- Mechanical Deformations: Engineers and designers use deformations to simulate how objects deform under stress or pressure. This is valuable in product design and manufacturing processes to predict and analyze the behavior of materials and structures.
- Virtual Prototyping: Deformations allow designers to create virtual prototypes of products, enabling them to test and refine designs before physical production.
- Medical Imaging and Simulation:
- Soft Tissue Simulation: In medical fields, deformations are applied to simulate the behavior of soft tissues in response to external forces. This is useful for medical training simulations, surgical planning, and virtual surgeries.
- Architectural Visualization:
- Realistic Environments: Deformations are utilized to create realistic and dynamic architectural environments. This includes the simulation of natural elements like water, vegetation, and atmospheric effects.
- Computer-Aided Design (CAD):
- Shape Modifications: Deformations are used in CAD software to modify and refine shapes during the design process. This is crucial for iterating on designs and exploring different configurations.
- Simulation and Scientific Research:
- Material Deformation: Deformations are applied to simulate the behavior of materials under various conditions, aiding scientific research in fields like physics and material science.
- Fluid Dynamics: Deformations play a role in simulating fluid flow, contributing to research in areas such as aerodynamics, weather modeling, and oceanography.
- Artistic Expression and Sculpting:
- Digital Sculpting: Artists use deformations to sculpt and mold digital models, creating intricate and expressive artworks. This is particularly evident in the fields of digital sculpting and concept art.
In essence, deformations are a fundamental aspect of 3D modeling and simulation, contributing to a wide array of applications that span entertainment, engineering, medicine, and beyond. Their versatility and ability to capture dynamic and realistic behaviors make them an indispensable tool across various industries.
Role Of Deformations in 3D Printing
Deformations play a crucial role in the realm of 3D printing, influencing the design, fabrication, and success of printed objects. Understanding how deformations can impact the 3D printing process is essential for achieving accurate and reliable results. Here are several aspects highlighting the role of deformations in 3D printing:
- Design Considerations:
- Thermal Deformations: During the 3D printing process, the material undergoes thermal changes as it is melted and then solidified. This can lead to thermal expansions and contractions, potentially causing deformations in the final printed object. Designers must account for these thermal effects in their models to ensure dimensional accuracy.
- Material Properties:
- Material Shrinkage: Different 3D printing materials exhibit varying degrees of shrinkage as they cool and solidify. Understanding the specific shrinkage characteristics of the chosen material is crucial for compensating in the design phase and achieving accurate dimensions in the final printed object.
- Printing Techniques:
- Layer Adhesion: In processes like Fused Deposition Modeling (FDM), where objects are built layer by layer, ensuring proper layer adhesion is critical. Insufficient adhesion between layers can result in weak structures and deformations in the final print. Adjusting print settings, such as layer height and temperature, can help mitigate these issues.
- Support Structures:
- Preventing Warping: Deformations, such as warping, can occur when certain sections of a printed object cool at different rates. Support structures are often used to minimize these deformations by providing additional stability to overhanging or delicate features during the printing process.
- Print Bed and Environmental Conditions:
- Bed Adhesion: Proper adhesion of the first layer to the print bed is crucial for preventing deformations. Factors like bed temperature, surface preparation, and environmental conditions in the printing area can affect adhesion and subsequent deformations.
- Post-Processing Techniques:
- Heat Treatment: Some 3D printed materials can undergo post-processing heat treatments to relieve internal stresses and reduce deformations. This is particularly important for materials like thermoplastics, which may experience residual stresses from the printing process.
- Iterative Prototyping:
- Evaluating Deformations: The iterative nature of 3D printing allows designers to evaluate prototypes and identify potential deformations. This feedback loop enables adjustments to the design, printing parameters, or material selection to address and minimize deformations in subsequent iterations.
- Advanced Printing Technologies:
- Resin-based Printing: In technologies like Stereolithography (SLA) or Digital Light Processing (DLP), where liquid resin is cured layer by layer, understanding the curing and solidification process is crucial to prevent deformations. Proper calibration and consideration of resin properties are essential.
- Simulation Software:
- Predicting Deformations: Simulation software can be employed to predict and analyze potential deformations in a 3D model before the actual printing process. This allows designers to make informed decisions and optimizations to reduce the likelihood of deformations in the final print.
Comprehensive understanding of deformations is essential for successful 3D printing. Designers and engineers need to consider material properties, printing techniques, support structures, and environmental conditions to minimize unwanted deformations and ensure the accuracy and reliability of the printed objects. Advances in technology and ongoing research continue to refine the 3D printing process, providing solutions to mitigate deformation challenges and enhance the overall quality of printed products.
Conclusion
Understanding and application of deformations in various fields of 3D modeling and simulation have become indispensable for achieving realism, functionality, and creativity. Deformations serve as a versatile toolset for artists, engineers, and researchers, allowing them to shape and animate objects in ways that closely mimic the behavior of real-world materials and structures.
In the realm of entertainment, deformations play a pivotal role in character animation, special effects, and virtual environments, contributing to the immersive experiences found in movies, video games, and virtual reality applications. These techniques enable the creation of lifelike characters, dynamic environments, and stunning visual effects that captivate audiences.
In engineering and industrial design, deformations are crucial for simulating the behavior of materials, predicting structural responses, and refining product prototypes. From mechanical simulations to virtual prototyping, the accurate representation of deformations aids in designing efficient and reliable systems, fostering innovation and optimization in product development.
Medical simulations benefit from deformations as well, allowing practitioners to simulate the behavior of soft tissues, aiding in surgical planning, training, and research. The ability to model realistic deformations contributes to advancements in medical technology and enhances the understanding of complex biological systems.
Moreover, in the field of 3D printing, understanding and mitigating deformations are essential for achieving precise and reliable results. Designers and engineers must carefully consider factors such as thermal effects, material properties, and printing techniques to ensure the dimensional accuracy and structural integrity of printed objects.
Overall, deformations serve as a bridge between the virtual and physical worlds, enabling the creation of realistic digital models that mirror the behavior of objects and materials in reality. As technology continues to advance, the role of deformations in 3D modeling and simulation is expected to evolve, offering even greater precision, efficiency, and creative possibilities across diverse applications and industries. Whether in entertainment, engineering, medicine, or design, the effective utilization of deformations continues to push the boundaries of what is possible in the three-dimensional digital realm.