3D printing, also known as additive manufacturing, is a revolutionary technology that has transformed the way we design, prototype, and manufacture objects. Unlike traditional manufacturing methods that involve subtracting material through processes like machining or molding, 3D printing builds objects layer by layer, allowing for intricate and complex geometries that were once difficult or impossible to achieve.
The fundamental concept behind 3D printing is the creation of a physical object from a digital model. This digital model, typically a Computer-Aided Design (CAD) file, serves as the blueprint for the 3D printer to follow. The 3D printer then translates this digital design into a tangible object by depositing material layer upon layer until the final form is achieved.
There are several types of 3D printing technologies, each with its own set of advantages and applications. Some of the most common 3D printing methods include:
- Fused Deposition Modeling (FDM): FDM is one of the most widely used 3D printing technologies. It involves the extrusion of thermoplastic filaments layer by layer to build up the object. This method is popular for its simplicity, cost-effectiveness, and versatility.
- Stereolithography (SLA): SLA uses a liquid resin that is cured, layer by layer, with the help of ultraviolet (UV) light. This process produces high-resolution prints with smooth surfaces, making it suitable for applications such as prototyping and jewelry design.
- Selective Laser Sintering (SLS): SLS employs a laser to sinter powdered material, typically nylon or metal, layer by layer. This technology is known for its ability to produce durable and functional prototypes and end-use parts.
- PolyJet Printing: PolyJet printers use inkjet technology to jet layers of liquid photopolymer onto a build platform. UV light cures each layer, resulting in highly detailed and multi-material prints. This method is often used in industries like dentistry and healthcare for creating accurate models.
- Binder Jetting: In binder jetting, a liquid binder is selectively deposited onto a powder bed, binding the particles together to form the desired shape. This process is employed in various materials, including metals and ceramics.
The applications of 3D printing are vast and continually expanding. It is widely used in industries such as aerospace, automotive, healthcare, and consumer goods. Prototyping remains one of the primary uses, allowing designers to quickly iterate and test concepts. However, the technology has evolved to the point where it is increasingly used for manufacturing end-use products and even construction components.
Beyond industrial applications, 3D printing has found its way into education, enabling students to explore concepts in a tangible way, and the consumer market, where hobbyists and enthusiasts can create custom designs at home.
As 3D printing technology continues to advance, the range of printable materials, including metals, ceramics, and bio-compatible substances, is expanding, opening new possibilities for innovation in various fields. The democratization of manufacturing through 3D printing is reshaping industries and empowering individuals to turn their ideas into reality with unprecedented ease and efficiency.
Types of 3D Printing Technologies
3D printing technologies, also known as additive manufacturing processes, encompass a diverse range of methods that enable the creation of three-dimensional objects layer by layer. Each type of 3D printing technology has its own unique advantages, applications, and materials. Here are some of the most prominent types of 3D printing technologies:
- Fused Deposition Modeling (FDM):
- Process: FDM is one of the most popular and accessible 3D printing technologies. It involves melting and extruding thermoplastic filaments through a heated nozzle, depositing layers onto a build platform.
- Materials: Common materials include PLA (Polylactic Acid), ABS (Acrylonitrile Butadiene Styrene), PETG, and more.
- Applications: Prototyping, concept modeling, and functional parts.
- Stereolithography (SLA):
- Process: SLA uses a liquid resin cured by a UV laser or light source. The laser selectively solidifies the resin layer by layer, creating precise and detailed objects.
- Materials: Resins with various properties, such as standard, flexible, or high-temperature resins.
- Applications: High-detail prototypes, jewelry, dental models, and intricate designs.
- Selective Laser Sintering (SLS):
- Process: SLS employs a high-powered laser to selectively fuse powdered materials (such as nylon or metals) layer by layer, forming a solid object.
- Materials: Nylon, metals (aluminum, titanium), ceramics, and more.
- Applications: Functional prototypes, end-use parts, and production of complex geometries.
- PolyJet Printing:
- Process: PolyJet technology jets layers of liquid photopolymer onto a build platform, and each layer is cured by UV light. It allows for the simultaneous use of multiple materials.
- Materials: Photopolymers with varying properties, including rigid, flexible, and transparent.
- Applications: Highly detailed and multi-material prototypes, visual models, and dental applications.
- Binder Jetting:
- Process: In binder jetting, a liquid binding agent is selectively deposited onto a powder bed, binding the particles together to form the object.
- Materials: Metals, ceramics, and sand.
- Applications: Metal parts for automotive and aerospace, sand molds for casting, and architectural models.
- Digital Light Processing (DLP):
- Process: Similar to SLA, DLP uses a digital light projector to cure liquid resin layer by layer.
- Materials: Resins similar to those used in SLA.
- Applications: Prototyping, jewelry, and dental applications.
- Material Jetting:
- Process: Material jetting involves jetting droplets of liquid photopolymer onto a build platform. UV light cures each layer, resulting in high-resolution prints.
- Materials: Photopolymers with various properties.
- Applications: High-detail prototypes, medical models, and dental applications.
- Directed Energy Deposition (DED):
- Process: DED uses a focused energy source, such as a laser or electron beam, to melt and deposit material, typically metal powders, layer by layer.
- Materials: Metals, including titanium, aluminum, and stainless steel.
- Applications: Metal part repair, large-scale metal fabrication, and aerospace components.
These 3D printing technologies offer a wide array of possibilities, enabling industries and individuals to produce objects with varying levels of complexity, precision, and material properties. As technology advances, new methods and materials continue to emerge, expanding the potential applications of 3D printing across various sectors.
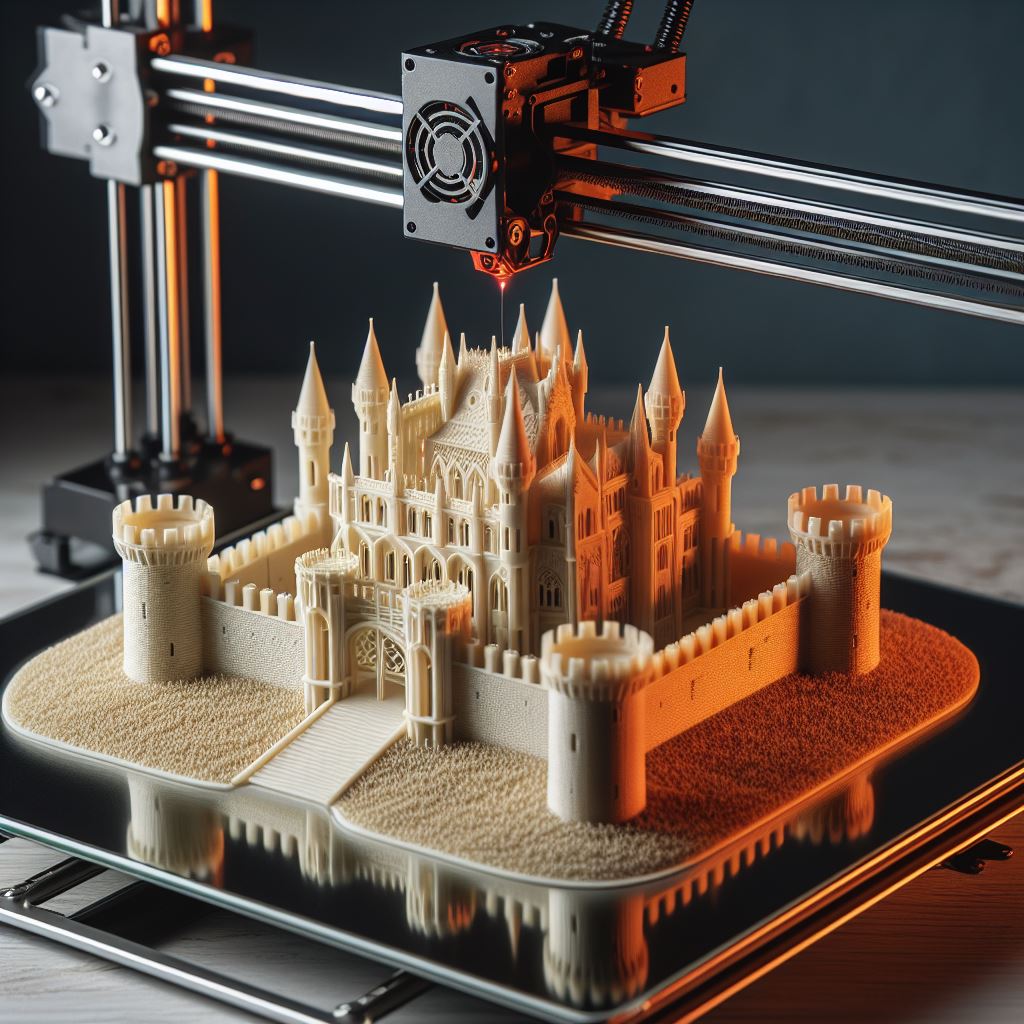
Key Components of a 3D Printer
A 3D printer is a sophisticated device that transforms digital designs into physical objects through additive manufacturing processes. Several key components work together to ensure the accurate and precise layer-by-layer construction of 3D-printed objects. Here are the key components of a typical 3D printer:
- Frame:
- The frame provides the structural foundation for the 3D printer, supporting all other components. It needs to be sturdy and rigid to minimize vibrations and ensure accurate prints.
- Print Bed:
- The print bed is the surface on which the 3D printer builds the object. It can be heated to help with material adhesion and prevent warping, particularly for materials like ABS.
- Extruder/Nozzle:
- The extruder is responsible for feeding and melting the filament (plastic material) before depositing it layer by layer. The nozzle determines the diameter of the extruded material and influences the layer resolution.
- Hotend:
- The hotend is the assembly that includes the nozzle and heating elements. It heats the filament to its melting point, allowing for controlled extrusion.
- Motion System:
- The motion system consists of motors, belts, and rods that control the movement of the print head (containing the extruder and nozzle) along the X, Y, and Z axes. Precise movement is crucial for accurate prints.
- Stepper Motors:
- Stepper motors drive the motion system, providing controlled and incremental movement. They allow for precise positioning of the print head and the build platform.
- Control Board/Controller:
- The control board interprets the G-code generated from the 3D model and coordinates the movement of the motors. It contains the firmware that controls the printer’s operation.
- Endstops/Limit Switches:
- Endstops or limit switches are sensors that detect the physical limits of the printer’s movement along each axis. They help the printer know when it has reached the end of a specific direction.
- Heated Bed (Optional):
- Some 3D printers feature a heated bed to improve adhesion and reduce warping. A heated bed can be particularly beneficial when working with materials like ABS.
- Build Plate:
- The build plate is the surface upon which the first layer of the print adheres. It is part of the print bed and can be removable in some printers, making it easier to remove finished prints.
- Cooling Fans:
- Cooling fans are used to regulate the temperature of certain components, such as the hotend and stepper motors, preventing overheating.
- LCD Display/Control Interface:
- An LCD display or control interface allows users to interact with the 3D printer, providing information about the printing process, temperature settings, and the ability to start, pause, or cancel a print.
- Power Supply:
- The power supply provides the necessary electrical power to operate the components of the 3D printer.
Understanding the functionality of these key components is essential for users, whether they are beginners or experienced enthusiasts, as it enables effective troubleshooting, maintenance, and customization of 3D printers for specific applications.
Materials Used in 3D Printing
Materials used in 3D printing, also known as filaments or resins, play a crucial role in determining the properties and applications of the final printed objects. The diverse range of materials available allows for the creation of prototypes, functional parts, and even end-use products. Here are some common materials used in 3D printing:
- PLA (Polylactic Acid):
- Type: Thermoplastic
- Properties: Biodegradable, environmentally friendly, and easy to print. PLA is often used for prototypes, hobbyist projects, and consumer goods.
- Applications: Concept models, figurines, and prototypes.
- ABS (Acrylonitrile Butadiene Styrene):
- Type: Thermoplastic
- Properties: Durable and impact-resistant. ABS requires a heated bed for printing to prevent warping.
- Applications: Functional prototypes, automotive parts, and consumer electronics.
- PETG (Polyethylene Terephthalate Glycol):
- Type: Thermoplastic
- Properties: Combines the strength of ABS with the ease of printing of PLA. PETG is known for its transparency, durability, and chemical resistance.
- Applications: Mechanical parts, containers, and outdoor prints.
- Nylon:
- Type: Thermoplastic
- Properties: High strength, flexibility, and durability. Nylon is suitable for applications requiring impact resistance and wear resistance.
- Applications: Gears, living hinges, and functional prototypes.
- TPU (Thermoplastic Polyurethane):
- Type: Flexible Thermoplastic
- Properties: Elastic and flexible. TPU is ideal for printing flexible parts and objects that require impact resistance.
- Applications: Phone cases, shoe insoles, and flexible prototypes.
- PLA+:
- Type: Modified PLA
- Properties: Enhanced PLA with improved strength and flexibility. PLA+ is designed to overcome some of the limitations of standard PLA.
- Applications: Durable prototypes, mechanical parts, and functional prints.
- Metal Filaments (e.g., PLA with Metal Particles, Metal Powders, or Metal-Clad Filaments):
- Type: Composite
- Properties: Contain metal particles for a metallic appearance. Post-processing methods can enhance the metallic finish.
- Applications: Decorative objects, jewelry, and sculptures.
- Wood Filaments:
- Type: Composite
- Properties: Contain wood fibers or particles, resulting in prints with a wood-like appearance and texture.
- Applications: Artistic models, decorative items, and prototypes with a natural aesthetic.
- Resin (for SLA and DLP Printers):
- Type: Liquid Photopolymer
- Properties: High resolution, smooth surface finish, and various material options, including standard, flexible, and castable resins.
- Applications: High-detail prototypes, dental models, and jewelry.
- Carbon Fiber Filaments:
- Type: Composite
- Properties: Reinforced with carbon fibers for increased strength and stiffness. Carbon fiber filaments are known for their lightweight and high-performance characteristics.
- Applications: Structural components, aerospace parts, and automotive applications.
- PEEK (Polyether Ether Ketone):
- Type: High-Performance Thermoplastic
- Properties: Excellent mechanical and thermal properties, chemical resistance, and biocompatibility. PEEK is used in demanding industrial applications.
- Applications: Aerospace components, medical implants, and high-performance prototypes.
- Ceramic Resins:
- Type: Resin
- Properties: Contain ceramic particles, providing heat resistance and electrical insulation.
- Applications: High-temperature components, electronic insulators, and ceramic-like prototypes.
As 3D printing technology continues to advance, the range of printable materials expands, offering new possibilities for innovation across various industries. Users can choose materials based on their specific requirements, whether it’s strength, flexibility, heat resistance, or aesthetic qualities.
Applications of 3D Printing
The applications of 3D printing, also known as additive manufacturing, span a wide range of industries and have transformative effects on the way products are designed, prototyped, and manufactured. The versatility and customization capabilities of 3D printing have led to innovative solutions in various fields. Here are some key applications:
- Prototyping:
- 3D printing is widely used in product development for rapid prototyping. It allows designers and engineers to quickly iterate and test their designs before moving to mass production, saving time and resources.
- Customized Products:
- The ability to create highly customized and personalized products is a significant advantage of 3D printing. This is evident in industries such as healthcare (custom implants and prosthetics), fashion (customized accessories and apparel), and consumer goods.
- Medical and Dental Applications:
- 3D printing has revolutionized the medical field. It is used to create patient-specific models for surgical planning, produce customized implants and prosthetics, and even generate tissues and organs for transplantation. In dentistry, it’s employed for creating dental crowns, bridges, and models for orthodontic treatment.
- Aerospace and Automotive Industries:
- Both aerospace and automotive industries leverage 3D printing for prototyping, creating lightweight components, and producing complex geometries that would be challenging with traditional manufacturing methods. This contributes to weight reduction, fuel efficiency, and improved performance.
- Tooling and Manufacturing Aids:
- 3D printing is employed to create custom tooling and manufacturing aids, such as jigs, fixtures, and molds. These tools enhance efficiency and precision in the production process.
- Education and Research:
- 3D printing is widely used in educational settings to teach students about design, engineering, and manufacturing. It provides a hands-on experience and allows students to turn their ideas into physical objects. In research, 3D printing is used to prototype experimental designs and create custom lab equipment.
- Architecture and Construction:
- In architecture, 3D printing is utilized for creating scale models, architectural prototypes, and even full-scale building components. Emerging technologies enable the construction of houses and structures layer by layer using large-scale 3D printers.
- Consumer Goods:
- 3D printing enables the production of custom consumer goods, ranging from fashion accessories to home decor items. Designers and artists can bring unique and intricate designs to the market, catering to individual tastes.
- Electronics and Wearables:
- 3D printing is used to produce casings and components for electronic devices and wearables. It allows for the creation of lightweight and compact designs with intricate features.
- Food Printing:
- In the food industry, 3D printing is employed to create edible designs using various ingredients. This includes chocolate, sugar, and other edible materials, offering new possibilities for culinary creativity.
- Art and Sculpture:
- Artists and sculptors use 3D printing to bring their imaginative creations to life. The technology allows for the realization of intricate and complex artistic designs that may be challenging or impossible with traditional methods.
- Environmental Applications:
- 3D printing can contribute to sustainable practices by reducing material waste. Additive manufacturing enables the creation of complex structures with minimal material usage, and recycled or bio-based filaments further enhance the eco-friendly aspects of 3D printing.
As technology advances, the applications of 3D printing continue to expand, offering innovative solutions and driving advancements in various industries. The ability to create prototypes and customized products quickly and efficiently has positioned 3D printing as a transformative force in the world of manufacturing and beyond.
Conclusion
In conclusion, the introduction of 3D printing marks a paradigm shift in the way we conceive, design, and manufacture objects. This transformative technology, also known as additive manufacturing, has transcended traditional manufacturing methods by enabling the layer-by-layer construction of intricate and complex structures. The diverse array of 3D printing technologies, ranging from Fused Deposition Modeling (FDM) to Stereolithography (SLA) and Selective Laser Sintering (SLS), offers unparalleled versatility in material usage and application.
The impact of 3D printing extends across various industries, from aerospace and healthcare to education and consumer goods. Its ability to facilitate rapid prototyping, customization, and the creation of intricate geometries has not only streamlined product development processes but has also opened new avenues for innovation. The democratization of manufacturing, allowing individuals and small businesses to turn digital designs into tangible objects, is a testament to the accessibility and democratizing influence of 3D printing.
As the technology continues to advance, with ongoing developments in materials, printing techniques, and the expansion of printable mediums to include metals, ceramics, and even biological materials, the potential applications of 3D printing seem boundless. From personalized medical implants to architectural marvels and artistic creations, 3D printing is breaking new ground and reshaping industries.
While challenges such as material limitations, printing speed, and post-processing requirements persist, the positive trajectory of 3D printing suggests a future where on-demand, customized manufacturing becomes the norm. The integration of 3D printing into mainstream production processes is not merely a technological advancement but a transformative force that empowers creativity, accelerates innovation, and paves the way for a more sustainable and adaptable approach to manufacturing in the years to come.