3D printing has revolutionized the way we create physical objects, allowing for the production of intricate and complex designs that were once difficult or impossible to achieve through traditional manufacturing methods. Blender, a powerful and open-source 3D modeling software, has become a popular choice for creating 3D printable models due to its versatility and robust feature set.
However, when it comes to 3D printing, there are certain constraints and considerations that designers must keep in mind to ensure successful and accurate prints. Blender provides tools and features to help users navigate these constraints and optimize their models for 3D printing.
1. Mesh Integrity: One of the primary constraints in 3D printing is ensuring the integrity of the mesh. 3D printers work by layering material on top of each other, and any issues with the mesh can result in print defects or failures. Blender offers various tools for mesh analysis and correction, such as the “Clean Up” options and the “Mesh Analysis” feature, which can help identify and fix issues like non-manifold geometry or intersecting faces.
2. Model Scale: Scale is a crucial factor in 3D printing. Many 3D printers interpret models in millimeters, so it’s essential to ensure that the scale of the model in Blender is accurate. Blender allows users to set the units for their projects, and it’s advisable to work in real-world units, such as millimeters or inches, to avoid scaling issues during the printing process.
3. Printable Supports: Some 3D prints require supports to prevent overhangs and ensure the stability of the model during printing. Blender has a built-in tool for generating supports, but it’s crucial to design models with consideration for where supports will be needed. Understanding the limitations of your 3D printer and optimizing your model’s geometry can help minimize the need for excessive supports, making the printing process more efficient.
4. Wall Thickness and Detail: The thickness of walls and level of detail in a model are critical considerations for 3D printing. Blender provides tools to measure wall thickness and ensure that it meets the minimum requirements for your 3D printer. Additionally, intricate details that are too small may not be accurately reproduced, so it’s essential to strike a balance between detail and printability.
5. Print Bed Size: The size of the 3D printer’s print bed imposes constraints on the maximum dimensions of the printable model. Blender allows users to set the scene’s dimensions and provides tools to visualize the printable area. Designers should be mindful of the print bed size and ensure that their models fit within these limits to avoid print failures.
While Blender offers a wide range of features for creating stunning 3D models, understanding and adhering to 3D printing constraints is crucial for successful prints. By addressing issues related to mesh integrity, scale, supports, wall thickness, and print bed size, designers can optimize their models for 3D printing and bring their creations to life with precision and accuracy.
Dimensional Accuracy and Tolerance
Dimensional accuracy and tolerance are critical considerations in 3D printing, where objects are built layer by layer through additive manufacturing processes. Achieving precise dimensions and understanding tolerances are crucial for ensuring that 3D-printed parts fit together correctly, meet design specifications, and perform their intended functions.
Dimensional Accuracy in 3D Printing:
Dimensional accuracy in 3D printing refers to how closely the physical dimensions of a printed object match the dimensions specified in the digital model. Various factors can influence dimensional accuracy in 3D printing:
- Printer Calibration: Proper calibration of the 3D printer is essential for achieving accurate results. Calibration ensures that the printer’s movements and extrusion of material are in line with the digital design.
- Material Shrinkage: Different 3D printing materials exhibit varying degrees of shrinkage as they cool. Understanding and compensating for this shrinkage in the design phase is critical for achieving accurate final dimensions.
- Layer Height: The layer height selected for the printing process affects the level of detail and accuracy. Smaller layer heights generally result in finer details but may also extend printing time.
- Printer Precision: The precision of the 3D printer’s movements and the resolution of its components, such as stepper motors, influence the accuracy of the printed object.
Tolerance in 3D Printing:
Tolerance in 3D printing represents the acceptable range of variation from the intended dimensions. It acknowledges that achieving perfect precision in every print is challenging due to the nature of the additive manufacturing process. Common factors affecting tolerance in 3D printing include:
- Print Material Properties: Different materials have unique characteristics, such as thermal expansion and contraction rates, which can affect tolerance. Designers must consider these material properties when setting tolerances.
- Printer Variation: Even well-calibrated printers may have inherent variations in print accuracy. Tolerance accounts for these variations, allowing for a margin of error.
- Print Orientation: The orientation of a part during printing can impact tolerances. Overhanging features or details may be affected by gravity and require supports, influencing the final dimensions.
Tips for Achieving Dimensional Accuracy and Tolerance in 3D Printing:
- Design Considerations: Design parts with appropriate tolerances, considering the material being used and the specific 3D printing technology. Rounded edges, chamfers, and fillets can enhance printability.
- Calibration: Regularly calibrate the 3D printer to maintain accuracy. This includes ensuring that the print bed is level, the extruder is properly calibrated, and the printer’s motion system is functioning correctly.
- Material Testing: Understand the properties of the chosen 3D printing material. Conduct test prints and adjust designs based on the material’s shrinkage and other characteristics.
- Print Settings: Fine-tune print settings such as layer height, print speed, and temperature to optimize dimensional accuracy. Experimenting with these settings allows for adjustments based on the desired level of precision.
- Post-Processing: Consider post-processing techniques, such as sanding or machining, to achieve tighter tolerances after printing.
Dimensional accuracy and tolerance are crucial aspects of 3D printing that demand attention from both designers and users. As the technology continues to evolve, understanding and addressing these factors will contribute to the advancement of reliable and accurate 3D-printed objects in various industries, from prototyping to customized production.
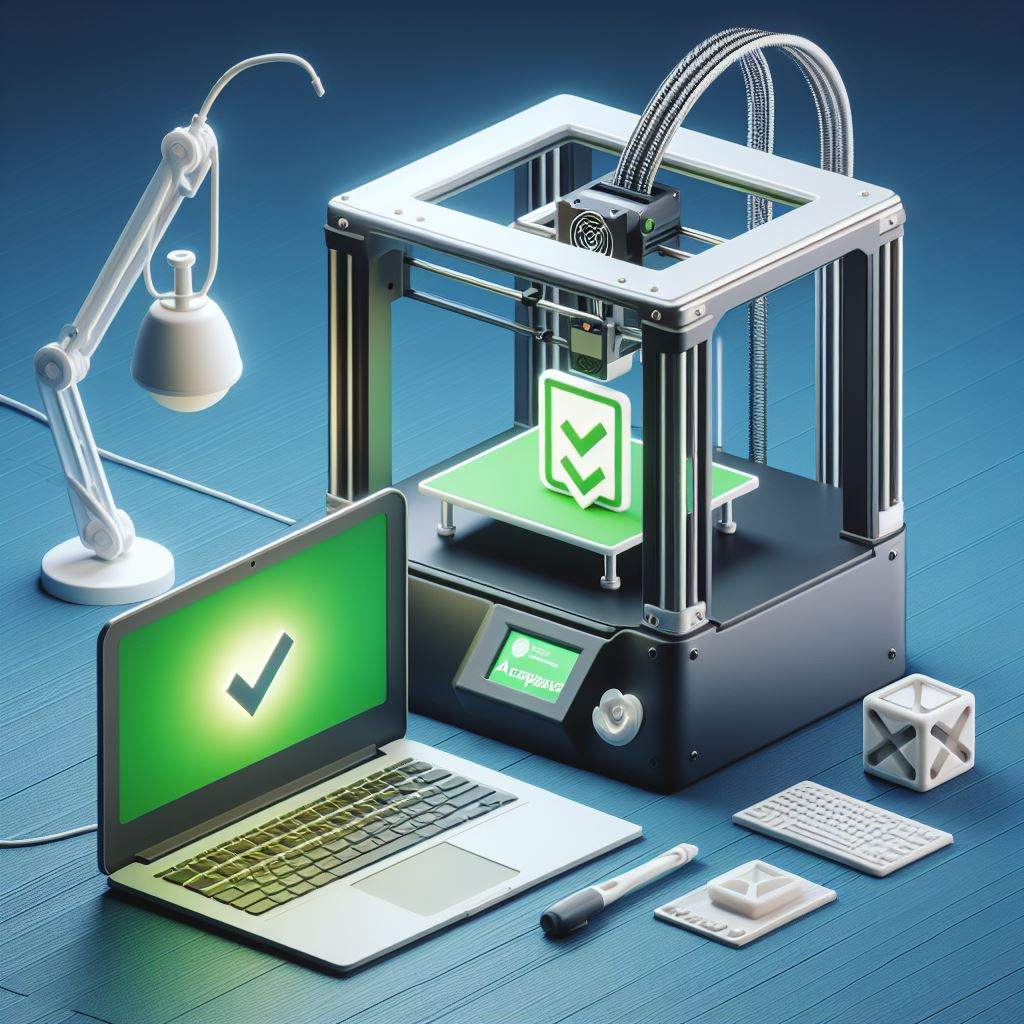
Print Orientation and Support Structures
In the world of 3D printing, the decisions made during the design and preparation stages can significantly impact the success of a print. Two crucial considerations are the print orientation and the need for support structures. Understanding how to optimize these aspects ensures better print quality, accuracy, and successful outcomes.
Print Orientation:
Print orientation refers to the positioning of a 3D model within the build volume of the 3D printer. The orientation chosen can have a substantial impact on the final print’s strength, surface finish, and the amount of support material required. Key factors to consider when determining the print orientation include:
- Overhangs and Support Requirements: Overhanging features, where the material has nothing beneath it, may require support structures. Orienting a model to minimize overhangs can reduce the need for supports, saving time and material.
- Layer Adhesion and Strength: The orientation affects layer adhesion and, consequently, the overall strength of the printed object. Consider the mechanical requirements of the part and orient it to optimize layer bonding.
- Surface Finish: Certain orientations may result in better surface finishes on specific areas of the model. Factors such as layer lines and support scars can be minimized or strategically placed based on print orientation.
- Print Time: Different orientations can significantly impact the time it takes to complete a print. The choice of orientation should balance print time with the desired quality.
Support Structures:
Support structures are temporary elements added to a 3D print to provide stability for overhanging features and prevent drooping or collapsing during the printing process. Considerations related to support structures include:
- Overhang Angle: Most 3D printers have a maximum overhang angle beyond which support structures become necessary. Understanding this angle is crucial for determining when and where supports are needed.
- Material and Printing Technology: The choice of 3D printing material and the printing technology employed influence the need for supports. Some materials and technologies allow for steeper overhangs without supports.
- Support Removal Difficulty: While supports are essential for certain geometries, removing them can be time-consuming and may leave marks on the finished part. Designers should consider post-processing efforts when planning for support structures.
- Custom Support Placement: Some slicer software allows for manual placement of support structures. This feature is beneficial when designers want to minimize support material usage or direct supports away from critical surfaces.
Tips for Optimizing Print Orientation and Support Structures:
- Use Support Only When Necessary: Minimize the use of supports by orienting the model to reduce overhangs. This not only saves material but also simplifies post-processing.
- Experiment with Orientations: Test different print orientations to find the optimal balance between print quality, strength, and print time.
- Leverage Software Features: Take advantage of advanced features in slicing software that allow for customized support structures and orientation adjustments.
- Consider Multi-Material Printing: Some advanced 3D printers support multiple materials in a single print. This capability can be leveraged to print support structures in a water-soluble material, simplifying post-processing.
Print orientation and support structures are integral aspects of successful 3D printing. A thoughtful approach to these considerations not only ensures better print quality but also optimizes material usage, print time, and post-processing efforts. As 3D printing technology continues to advance, refining these techniques contributes to the realization of more complex and high-quality printed objects.
Wall Thickness and Structural Integrity
Wall thickness is a critical aspect of 3D printing design that directly influences the structural integrity of printed objects. Achieving the right balance between wall thickness and structural requirements is crucial for producing functional and robust 3D-printed parts across various applications, including prototyping, manufacturing, and rapid product development.
Importance of Wall Thickness:
- Stability and Strength:
- Sufficient wall thickness is essential for providing stability and strength to 3D-printed objects. Thin walls may result in a lack of structural integrity, making the printed part prone to deformation or breakage.
- Printability:
- The chosen wall thickness affects the printability of the object. Extremely thin walls may be challenging to print accurately, leading to issues such as warping, layer separation, or print failure.
- Material Characteristics:
- Different 3D printing materials have unique characteristics, and the appropriate wall thickness depends on the material being used. Some materials may require thicker walls to ensure adequate strength and durability.
- Functionality:
- The intended function of the printed part influences the required wall thickness. Functional components, such as load-bearing structures or parts subject to mechanical stress, generally need thicker walls to meet performance requirements.
Considerations for Wall Thickness:
- Material Guidelines:
- Refer to material guidelines provided by the filament or resin manufacturer. These guidelines often include recommended minimum and optimal wall thickness values for specific materials.
- Print Technology:
- The 3D printing technology used (e.g., Fused Filament Fabrication, Stereolithography) can impact the achievable wall thickness. Some technologies may offer higher precision for thin walls, while others may have limitations.
- Object Geometry:
- The geometry of the object plays a significant role in determining the appropriate wall thickness. Complex geometries or intricate details may require adjustments to wall thickness to ensure structural integrity.
- Layer Height and Resolution:
- The chosen layer height and print resolution influence the precision of each layer. Thinner layers generally allow for more detailed prints, but the overall wall thickness should be adjusted accordingly to maintain structural integrity.
Optimizing Wall Thickness for Structural Integrity:
- Design for Purpose:
- Understand the intended use of the printed object. Design components with the required level of structural integrity based on the expected loads, stresses, and environmental conditions.
- Reinforcement and Support:
- Reinforce critical areas or features with additional material or structures. This can enhance the overall strength of the part without uniformly increasing wall thickness.
- Gradual Transitions:
- Use gradual transitions in wall thickness to avoid sudden changes that may lead to weak points or stress concentrations. Smooth transitions contribute to a more uniform distribution of stress.
- Iterative Testing:
- Conduct iterative testing with prototypes to assess the structural performance. Adjust the wall thickness based on testing results and feedback, refining the design for optimal structural integrity.
- Software Analysis:
- Utilize 3D modeling software that offers structural analysis tools. These tools can simulate how different wall thicknesses will perform under specific conditions, helping designers make informed decisions.
Achieving the right wall thickness is a delicate balance that requires careful consideration of material properties, print technology, and the functional requirements of the printed object. By paying attention to these factors and optimizing the design iteratively, designers can ensure the structural integrity of 3D-printed parts, leading to successful and reliable outcomes in various applications.
Conclusion
Understanding 3D printing constraints is paramount for achieving successful and reliable outcomes in the world of additive manufacturing. As we explored various facets such as dimensional accuracy, tolerance, print orientation, support structures, and wall thickness, it becomes evident that each plays a crucial role in the overall performance of a 3D-printed object.
Dimensional accuracy and tolerance are the cornerstones, ensuring that the digital design seamlessly translates into a physical reality while accounting for the inherent variations introduced by the 3D printing process. Print orientation and support structures add a layer of complexity, requiring thoughtful considerations to optimize for quality, print time, and material efficiency. Meanwhile, the delicate balance between wall thickness and structural integrity is key, influencing the stability and strength of the final product.
In the dynamic field of 3D printing, where innovation and creativity thrive, designers and engineers must navigate these constraints with precision. Embracing best practices, leveraging advanced software tools, and embracing an iterative design process are essential strategies. The constant interplay between design intent, material characteristics, and the capabilities of the chosen 3D printing technology ultimately determines the success of a print.
As the technology continues to evolve, a nuanced understanding of these constraints empowers creators to push the boundaries of what is possible. It enables the production of intricate prototypes, functional components, and custom designs with greater accuracy, efficiency, and reliability. In essence, mastering 3D printing constraints opens up a world of possibilities, where imagination meets precision to shape the future of manufacturing and design.