Support structures play a crucial role in the realm of 3D printing, providing a foundation for the successful fabrication of intricate and complex designs. As the name suggests, support structures are additional elements that help uphold overhanging features and prevent sagging or collapse during the printing process. Understanding the significance of supports and their various types is essential for achieving high-quality and accurate 3D prints.
Importance of Supports:
- Overhangs and Bridges:
- 3D printers build objects layer by layer. When a layer contains elements that extend outward without a solid foundation beneath them, such as overhangs or bridges, the molten material may not have sufficient support, leading to deformities in the print.
- Printing in Mid-Air:
- Supports provide a temporary structure for the printer to deposit material on, ensuring that each layer has a stable base. Without supports, the printer would essentially be attempting to print in mid-air for certain sections of the model.
- Complex Geometries:
- Intricate designs with complex geometries often feature angles and curves that defy the natural stacking ability of the 3D printing process. Supports enable the printer to construct these challenging shapes accurately.
Identifying Overhangs and Unsupported Features
Identifying overhangs and unsupported features is a critical step in the 3D printing process to ensure the successful fabrication of intricate and complex models. Overhangs are sections of a 3D model that extend outward at an angle beyond what the printing material can naturally support. Unsupported features are elements of a design that lack a solid foundation beneath them. Recognizing and addressing these aspects are essential for achieving high-quality prints and avoiding structural issues. Here’s a guide on how to identify overhangs and unsupported features in your 3D models:
1. 3D Printing Software:
Most 3D modeling and printing software includes features to identify and visualize overhangs and unsupported regions. These tools help users identify areas in the model that may require support structures.
2. Overhang Angle:
Overhangs are typically defined by a specific angle. As a general rule, overhangs greater than 45 degrees are likely to require support. Many slicing software programs allow users to set a threshold angle for automatic support generation.
3. Slicing Preview:
Before initiating the 3D printing process, use the slicing software to generate a preview of the print layers. This preview can highlight overhangs and unsupported features layer by layer, allowing you to identify potential issues before printing.
4. Manual Inspection:
Carefully inspect your 3D model visually or within the 3D modeling software. Look for sections where the model extends outward without proper support. Rotate and view the model from different angles to identify areas that may need attention.
5. Simulation Tools:
Some advanced 3D printing software and online services provide simulation tools. These tools can simulate the printing process and highlight areas prone to issues, such as overhangs, warping, or other structural concerns.
6. Experience and Trial:
Over time, with experience, you’ll develop an intuition for recognizing potential overhangs and unsupported features in your 3D models. Trial and error, combined with iterative improvements, will enhance your ability to create models that print successfully without compromising quality.
7. Model Orientation:
The orientation of the 3D model on the print bed plays a crucial role in determining the need for supports. Experiment with different orientations to minimize overhangs or strategically position them to reduce the necessity for extensive supports.
8. Fillet and Chamfer:
When designing your 3D model, consider incorporating fillets and chamfers to round off sharp edges. This design technique can help reduce the severity of overhangs, making them more manageable without the need for extensive support structures.
9. Layer-by-Layer Analysis:
Examine your model layer by layer to identify areas where overhangs may occur. Understanding the layering process allows you to anticipate potential challenges and implement design modifications or support structures as needed.
10. Support Generation Tools:
Utilize the automatic support generation tools provided by your slicing software. These tools analyze the geometry of the model and generate supports where necessary. Adjust settings to control the density and placement of supports.
By employing a combination of these methods, 3D printing enthusiasts and professionals can effectively identify overhangs and unsupported features in their models. This proactive approach helps streamline the printing process, minimize the need for excessive supports, and ultimately leads to more successful and visually appealing 3D prints.
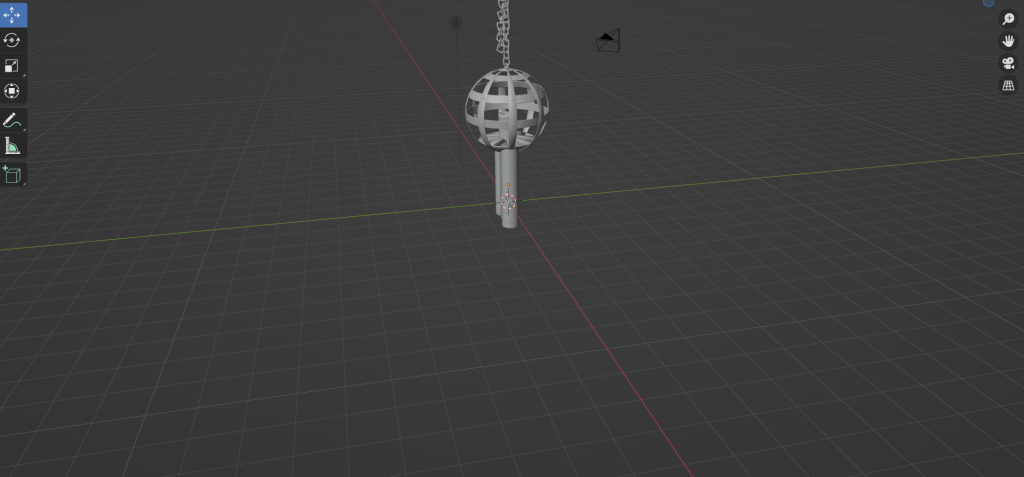
Using the Support Structures Tool
Support structures are a crucial element in 3D printing, particularly when dealing with overhangs and intricate designs. In Blender, a versatile and powerful 3D modeling software, the use of support structures is facilitated through various tools. Although Blender doesn’t have a dedicated “support structure tool” like some specialized 3D printing software, you can achieve effective support generation using a combination of features. Here’s a guide on how to use support structures in Blender:
1. Enable the 3D Printing Toolbox:
- Start by enabling the 3D Printing Toolbox add-on in Blender. Go to “Edit” -> “Preferences” -> “Add-ons” -> Search for “3D Printing Toolbox” and enable it. This toolbox provides features useful for 3D printing, including support generation.
2. Check Overhangs:
- In the 3D Printing Toolbox, there’s a “Check All” button that performs various checks on your model, including identifying overhangs. This tool helps you visually inspect and identify areas that may need support.
3. Enable Face Orientation:
- To visualize potential issues with face orientation, go to the “Overlays” dropdown menu in the 3D Viewport and enable “Face Orientation.” This helps you identify faces that might cause printing issues due to improper orientation.
4. Manual Support Structure Creation:
- Blender allows you to manually create support structures by adding additional geometry to your model. You can use the “Mesh” -> “Cube” or “Mesh” -> “Cylinder” tools to create simple support structures where needed.
5. Use the Boolean Modifier:
- The Boolean modifier in Blender can be employed to intersect a simple geometric shape (like a cube) with your model, creating support structures where needed. This process involves duplicating the model, scaling it down, and using the Boolean modifier set to “Intersect.”
6. Sculpt Mode for Custom Supports:
- Blender’s Sculpt mode can be a powerful tool for customizing your support structures. You can use the “Draw” or “Grab” brushes to manually sculpt supports in areas that require additional reinforcement.
7. Mesh Analysis:
- Blender has various mesh analysis tools that can help you identify potential printing issues. These tools can be found in the “N” panel under the “Item” tab. The “Clean Up” and “Degenerate Dissolve” options can be particularly useful.
8. Print Test Renders:
- Before exporting your model for 3D printing, consider using Blender’s rendering capabilities to create test renders. This can help you visually inspect your model for any potential issues before committing to the printing process.
9. Export with Supports:
- When you’re satisfied with your model and the added support structures, export it in a format compatible with your 3D printer. Common formats include STL or OBJ. Ensure that your 3D printer software recognizes the support structures in the exported file.
While Blender might not have a dedicated support generation tool, its robust set of modeling and sculpting features provides ample flexibility for creating effective support structures. By combining these features and taking advantage of the 3D Printing Toolbox, Blender users can produce high-quality 3D prints with well-managed support structures.
Optimizing Support Structures
Optimizing support structures is a critical aspect of 3D printing, as it directly influences the success of printing complex and overhanging geometries. Effective support optimization ensures minimal material usage, faster print times, and easier post-processing. Here’s a guide on how to optimize support structures for your 3D prints:
**1. Consider Print Orientation:
- The orientation of your 3D model on the print bed significantly impacts the need for supports. Experiment with different orientations to find the one that minimizes overhangs and reduces the dependency on support structures.
2. Utilize Automatic Support Generation:
- Most 3D printing software includes automatic support generation tools. Enable these features and adjust parameters like support density and overhang angle to optimize the generation of supports based on your specific model.
3. Manual Support Placement:
- For fine-tuning, consider manually placing supports using your 3D printing software. This allows you to strategically position supports where they are most needed and avoid over-supporting areas that may not require it.
4. Gradual Support Angles:
- Gradually increasing the overhang angle threshold for support generation can help create more efficient supports. Instead of a single sharp threshold, a gradual increase allows for more nuanced support placement.
5. Use Dissolvable Supports:
- If your 3D printer supports multiple materials, consider using a dissolvable support material. This allows for easy removal of supports without manual intervention, resulting in a cleaner finish on your printed model.
6. Adjust Support Infill Percentage:
- Some slicing software allows you to control the infill percentage of the support structures. Lowering the infill percentage can reduce material usage while still providing sufficient support for your print.
7. Tree Support Structures:
- Some advanced slicing software features tree-like support structures. These structures use less material and provide effective support where needed. Experiment with different tree support options to find the one that works best for your model.
8. Mesh Analysis and Cleanup:
- Before generating supports, analyze your 3D model for potential issues using mesh analysis tools. Cleaning up the mesh by removing unnecessary geometry can reduce the need for excessive supports.
9. Custom Support Structures:
- In some cases, manually adding custom support structures using your 3D modeling software can be more efficient than relying solely on automatic tools. This approach allows for precise support placement in critical areas.
10. Print Test Models:
- Before committing to a full-scale print, consider printing a small test model with optimized supports. This allows you to evaluate the effectiveness of the supports and make adjustments as needed without wasting a significant amount of material.
11. Post-Processing Considerations:
- When optimizing supports, also consider how easily they can be removed during post-processing. Striking a balance between robust support during printing and easy removal afterward is crucial for achieving a clean and polished final product.
12. Iterate Based on Results:
- 3D printing often involves an iterative process. After printing, evaluate the results, and if necessary, make adjustments to your support optimization strategy for future prints.
By implementing these optimization techniques, you can strike a balance between providing adequate support for your 3D prints and minimizing the impact on print quality, material usage, and post-processing efforts. Adjusting support parameters and experimenting with different settings will help you achieve optimal results for your specific models and 3D printing requirements.
Conclusion
Process of adding supports in Blender is a vital step in ensuring the successful 3D printing of intricate and complex models. While Blender may not have a dedicated “support structure tool,” its versatile set of modeling and sculpting features provides users with the tools needed to create effective supports. By enabling the 3D Printing Toolbox, checking for overhangs, and utilizing manual techniques such as the Boolean modifier or sculpting in Blender, users can strategically reinforce their models where necessary.
Optimizing support structures involves a thoughtful balance between automatic generation and manual placement, considering factors such as print orientation, overhang angles, and support infill percentage. The ability to experiment with different support options and orientations allows users to find the most efficient and material-friendly configuration for their specific models.
As technology advances, Blender users can also benefit from continuous updates and improvements, potentially introducing more specialized tools or features for streamlined support generation. Nevertheless, the current capabilities of Blender, combined with a user’s creativity and attention to detail, empower them to create high-quality 3D prints with well-managed support structures.
In the ever-evolving landscape of 3D printing, Blender remains a powerful tool for both modeling and preparing models for physical realization. With a comprehensive understanding of how to identify, add, and optimize supports in Blender, users can confidently navigate the intricacies of 3D printing, producing impressive and flawless prints that bring their digital designs to life.